Continuous Improvement Manager
Ferrara
Fecha: hace 4 días
ciudad: Reynosa, Tamaulipas
Tipo de contrato: Tiempo completo
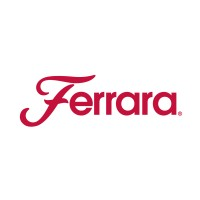
Job Location: Reynosa
This position is based in Reynosa, Tamaulipas, Mexico. A valid visa or the ability to obtain one to travel to the US is required.
Want to make an impact?
The Continuous Improvement Manager will build and sustain a continuous improvement culture across all levels of the factory using a variety of continuous improvement tools. This individual will work cross functionally using strong communication skills to instill a culture focused on prioritizing top losses and using strong analytical skills to improve safety, quality, cost, and OEE on a daily basis
Ways you will make a difference
This position is based in Reynosa, Tamaulipas, Mexico. A valid visa or the ability to obtain one to travel to the US is required.
Want to make an impact?
The Continuous Improvement Manager will build and sustain a continuous improvement culture across all levels of the factory using a variety of continuous improvement tools. This individual will work cross functionally using strong communication skills to instill a culture focused on prioritizing top losses and using strong analytical skills to improve safety, quality, cost, and OEE on a daily basis
Ways you will make a difference
- Champion Continuous Improvement and TPM methodologies along with a Lean mindset across the facility
- Deploys strategic methodologies, systems, and tools including Autonomous Maintenance, Preventative Maintenance, SMED, Problem Solving, Green Belt/Black Belt Project, and Process Mapping to deliver site OEE and cost savings goals
- Drives and supports cost ideations and diagnostics, along with tracking projects for visibility
- Provides tracking and regular communication to various plant functions and teams regarding Manufacturing Reliability progress
- Integrates system health and project monitoring into current structure (COE meetings, Operational Reviews) to ensure sustainability of improvements
- Identifies and troubleshoot chronic and sporadic losses by engaging and collaborating with hourly personnel and supervisors. Drives losses to zero using SPC, Six Sigma and other lean principles
- Utilizes systems and tools to deliver a reduction in minor stops and breakdowns
- Drives restoration to base condition of bottleneck equipment through AM and PM execution (CILs, Centerlines, Defect Identification, 5S, Visual Management)
- Builds capability in the PM team to effectively plan, schedule, and execute work; install and sustain the Breakdown Elimination and equipment classification systems
- Identifies and implements new technology improvements
- Builds capability by developing and executing training for operations, leadership and plant associates on methodologies, systems, and tools
- Supports plant implementation of AM and PM by coaching supervisors/ managers to ensure their capability to lead work teams
- Promotes a change of culture within the group/site – especially at the front-line level
- Lead and coach projects that align with key priorities and help develop strategic plans to ensure that manufacturing sites achieve their goals
- Guide the plant floor data standardization, collection, utilization, and management to drive continuous improvement
- Develop and mentor professional growth and advancement of departmental staff
- Train and support managers and supervisors as necessary
- Excellent problem-solving skills
- Analytically minded
- Ability to communicate effectively with all levels of the organization
- Ability to plan and manage priorities
- Ability to lead cross-functional teams across all levels of the organization
- Ability to influence without authority
- Building effective relationships amongst all levels of the organization
- Being a change management agent
- Bachelor’s degree in Industrial Engineering, Manufacturing Engineering, or technical/business field
- 5+ years of continuous improvement experience in a manufacturing environment
- 2+ years of leadership experience and managing direct reports
- Experience leading continuous improvement projects (Lean, TPM, Six Sigma)
- Proficiency in Microsoft Office Suite
- Food manufacturing background preferred
- General knowledge of ERP systems; SAP experience preferred
- Formal Lean Six Sigma experience preferred
- Willingness to travel to Ferrara factories in Mexico and the U.S.
Ver más empleos en Reynosa, Tamaulipas